Mannheim, 18.03.2020
Especially energy-intensive industries benefit greatly from an internal power plant that generates the electricity for the operations and enables demand-oriented feed-in. The production processes of construction material and basic chemicals consume a lot of energy, which, besides the labor expenses, represent one of the main cost factors in the energy-intensive industries. The integration of internal cogeneration power plants enables plant operators to generate their own power and optimize production processes, thereby achieving significant operating cost savings and enhanced security of supply. In view of their mode of operation, efficiency, and structural properties, cogeneration power plants in an output range of 400 to 10,300 kWel are especially attractive for medium-sized industrial enterprises. Empirical values, e.g. those provided by the energy provider MVV Energie AG in Mannheim, show that for a cogeneration power plant to be profitable, it should operate for at least 5,000 of the year’s 8,760 hours (55 to 60 percent).
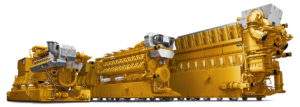
Get Ready for the Future with Cogeneration
Gas engines and power gensets for cogeneration power plants are available for a wide output spectrum. Thus, power plants of different sizes and output categories can be implemented for a variety of application scenarios. High-output cogeneration power plants can be deployed by district heat providers, municipal energy providers, industrial enterprises, and other large companies. Smaller cogeneration power plants can be used e.g. in schools, hotels, office buildings, or tradesmen’s firms.
Cogeneration power plants can run on various fuels, including natural gas, liquefied gas, plant gas, plant oil, and fuel oil. Compared to the separate generation of electrical energy and heat, combined heat and power (CHP) plants make much better use of the primary energy. The cogeneration power plants of Caterpillar Energy Solutions’ product brands Cat and MWM enable economic, efficient energy generation. The on-site plant transforms the employed energy into electrical energy and heat. The resulting exhaust heat can be reused directly and is not lost. In the trigeneration concept, the heat generated by the trigeneration plant is used to run an adsorption refrigerator. The use of the exhaust heat from the trigeneration power plant instead of electricity for cooling purposes reduces the company’s air-conditioning power costs, thereby greatly improving the profitability of the trigeneration power plant. Trigeneration can be used wherever there is a need for cooling. This includes cold chains in the food production and the air-conditioning of offices, greenhouses, and medical facilities.
Significant Cost Reduction and Security of Supply
Especially companies that depend on a steady power supply, such as medical facilities or industrial enterprises that operate in shifts, benefit from the security of supply that is possible with an internal cogeneration power plant. The emergency power supply with an international cogeneration power plant represents a significant benefit for companies and institutions for which constant power supply is vital. The higher the electricity prices, the more economic an internal cogeneration power plant gets for the plant operators, as the internal cogeneration power plant gives them more independence from the grid, from the power price development, and from daily exchange prices. The operator can save even more if he is able to use raw materials that accumulate in his production. On a long-term basis, operators can reduce their power and heat costs by flexibilizing their cogeneration power plant to enable demand-oriented power generation. Especially commercial and industrial enterprises with shift operation benefit from the flexible, demand-oriented energy generation by their own cogeneration power plant.
Through the installation of heat storage units, it is also possible to buffer any fluctuations in the demand for energy. Apart from the electricity cost savings achieved through the internal generation, CHP plant operators can save heating costs and generate income by selling excess electricity, in which case they may also benefit from a surcharge according to the German Combined Heat and Power Act (KWKG). Since January 1, 2019, the Germany Energy Collection Act (EnSaG) requires even small power generators to record on a daily basis whom they supply their power to and report this to the Federal Network Agency. The feed-in and sale of excess energy to local and district heat networks and power grids increases the profitability both of the cogeneration power plant and of the company itself.
Cogeneration for Sustainable Energy Generation
In this age of renewable energies, the need for sustainable power generation is on the rise. In accordance with the defined climate protection goals, the Integrated Energy and Climate Program (IEKP) of Germany’s federal government provides for a 40-percent reduction in emissions by 2020 compared to 1990. In the field of energy supply, the increased and efficient use of CHP plants can greatly contribute to the reduction of emissions that harm the environment. Cogeneration enables the distributed generation of power and heat right where they are needed. In contrast to separate generation, CHP plants lose far less energy in the generation process. Along with the lower carbon emissions, this makes cogeneration a sustainable alternative for plant operators.
With its product brands Cat and MWM, Caterpillar Energy Solutions offers an extensive range of gas engines, power gensets, and turnkey CHP plants that meet highest quality requirements as well as international pollution and fuel consumption standards. In the field of highly efficient, ecologically advanced distributed energy solutions, Caterpillar Energy Solutions has become a market leader that is a reliable partner for demonstrable, sustainable added value in distributed energy generation around the globe.